An ecient self-circulating sand mill specically designed for university research and industrial pilot-scale development.
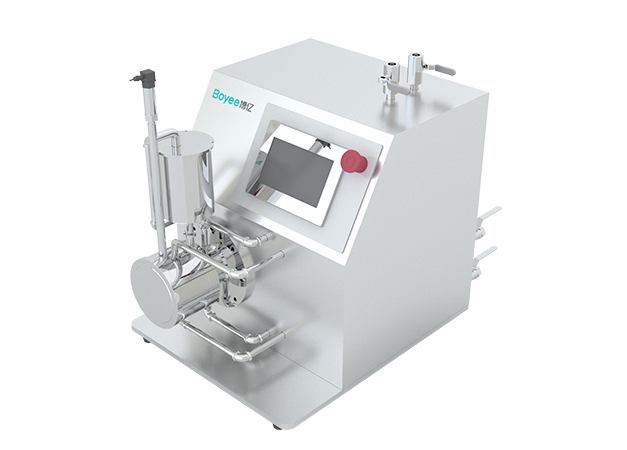
boyi@Building 7, Xiaweishui Industrial Zone, Hongqiaotou Community, Yanluo Street, Bao'an District, Shenzhen
An ecient self-circulating sand mill specically designed for university research and industrial pilot-scale development.
Silicon Carbide (SiC) Chamber Lining: Combined with guided ow channels to create axial vortex ow, enhancing grinding eciency. Optimized Material Flow: Engineered channels direct slurry movement for maximum particle interaction.
Centrifugal Pumping Eect: Rotor-generated suction works with stack-disc lters to create autonomous circulation. Zero-Residue Advantage: Eliminates material retention and cross-batch contamination.
Zirconia (ZrO2) Filter Design: 40% increased ow area. Clog-Free Operation: Combines rotor centrifugal force with static separation to prevent media blockage.
Spindle Speed
Zirconia Bead Diameter
Bead Filling QTY
Energy Consumption
Batch Capacity
The grinding system can choose turbine and rod pin according to the requirements:
扫码关注