Its core advantages lie in refining or improving medium precision and particle refinement, making it suitable for processing high-temperature materials, ceramic fibers, metal oxides, and other wear-resistant applications.
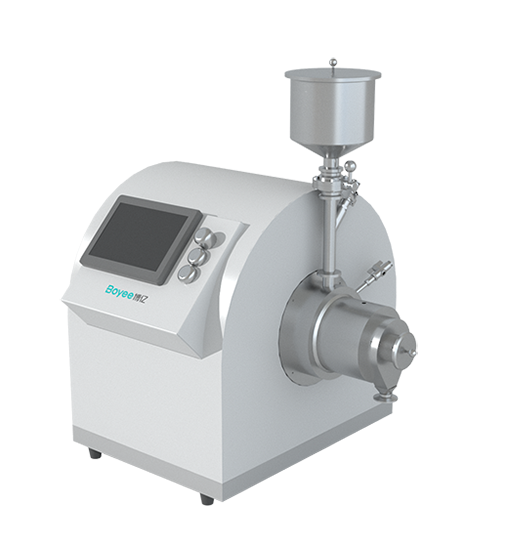
boyi@Building 7, Xiaweishui Industrial Zone, Hongqiaotou Community, Yanluo Street, Bao'an District, Shenzhen
Its core advantages lie in refining or improving medium precision and particle refinement, making it suitable for processing high-temperature materials, ceramic fibers, metal oxides, and other wear-resistant applications.
Asymmetric membrane design and plastic flow separation device; spindle speed: Φ590/1min; impeller speed: 4~6m/s; bidirectional vortex formed by counter-rotation.
Oxidation filter (pore size gradient design) with maximum surface density processing and filling performance (>99.2%).
The labyrinth seal adopts precision axial radial gap control (0.05-0.1mm) and multi-stage meandering runner design, forming an ecient pneumatic barrier under 0.3MPa gas pressure.
Spindle Speed
Bead Diameter
Bead Loading
Energy Consumption
Optimal Batch Capacity
The grinding system can choose turbine and rod pin according to the requirements:
扫码关注